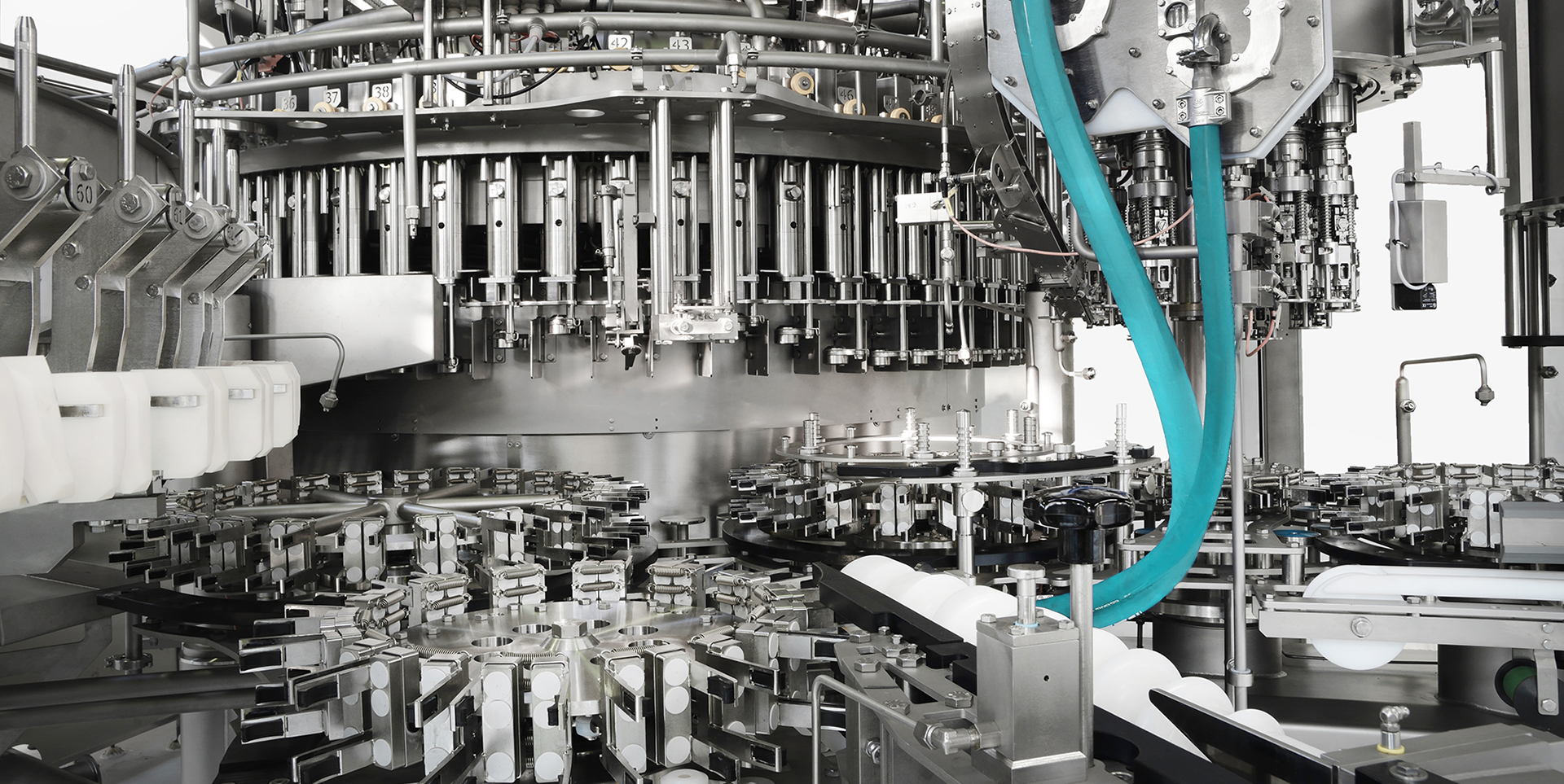
COMPANY
With a dedicated team of highly experienced employees, we try to push the limits of our imagination to get the best problem-solving ideas. At Vipoll we think, that a solution is a mutually agreed-upon answer to a recognized problem. Therefore, our customers and the obstacles in their way to success, stand at the core of our focus.
In the process of bringing a solution to life, we have a team of project managers, engineers and technicians who have years of experience and know-how, especially in food and beverage industries, as well as other industries. Together with our respected partners, we deliver a complete technical and commercial solution in the form of turnkey projects for complete bottling lines and end-of-line packaging systems as well.
Our commitment to continuous development of project management organization and company culture will enable us to meet all customer requirements on time, within agreed specification and on budget.
SOLUTIONS
HOW ARE YOU FILLING TODAY?
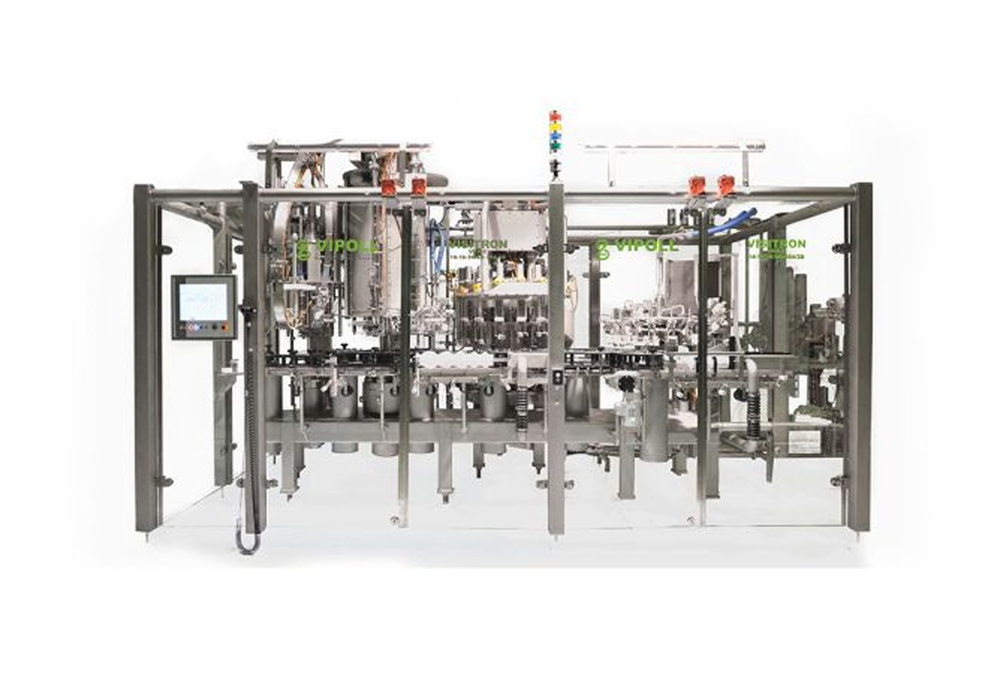
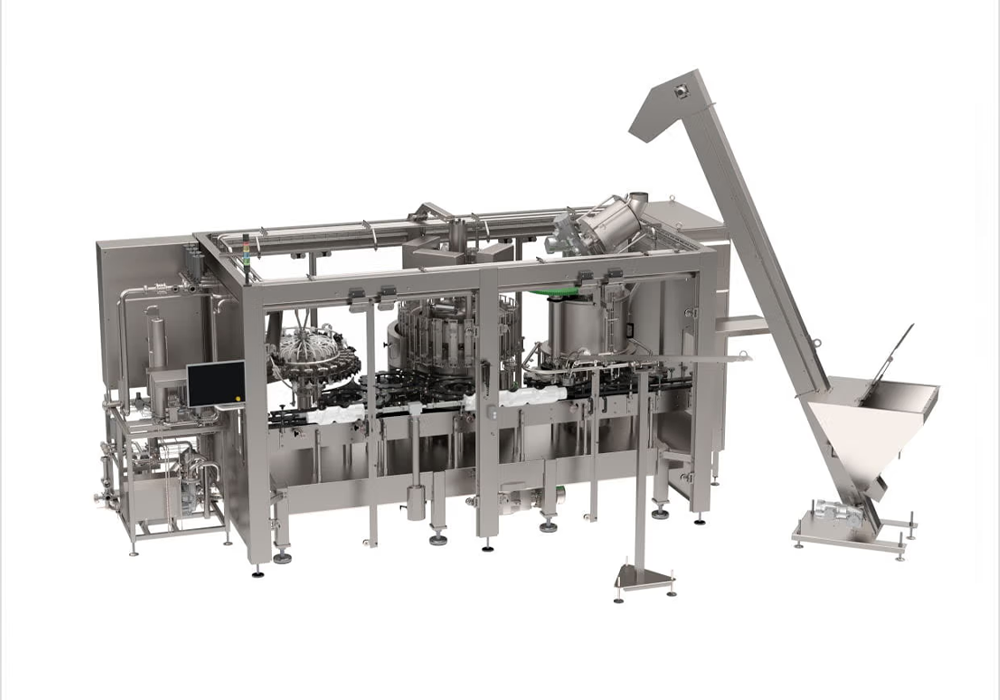
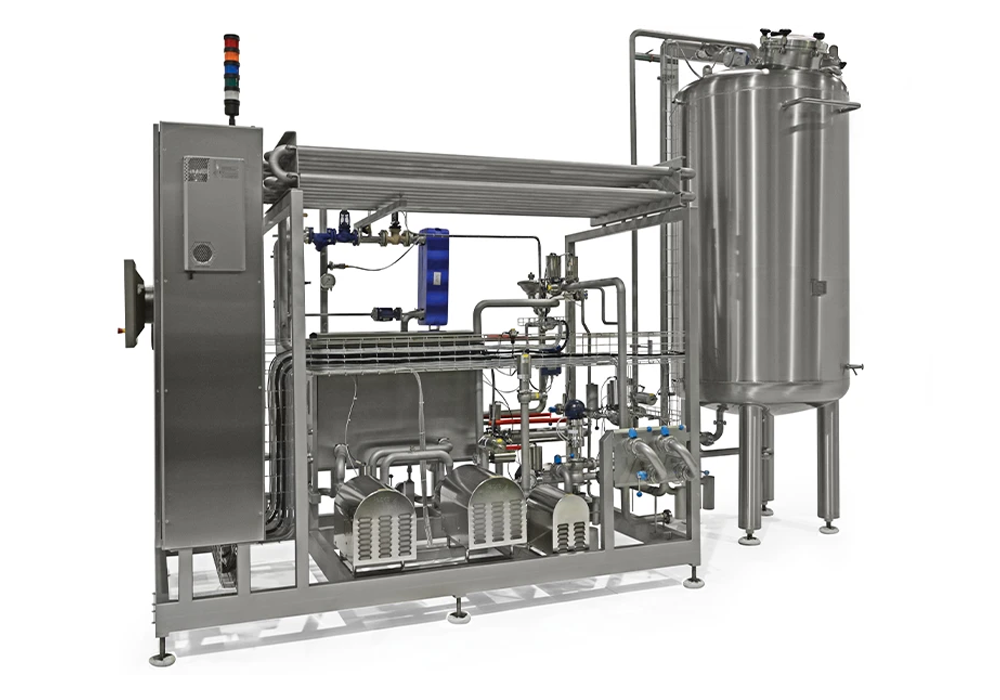
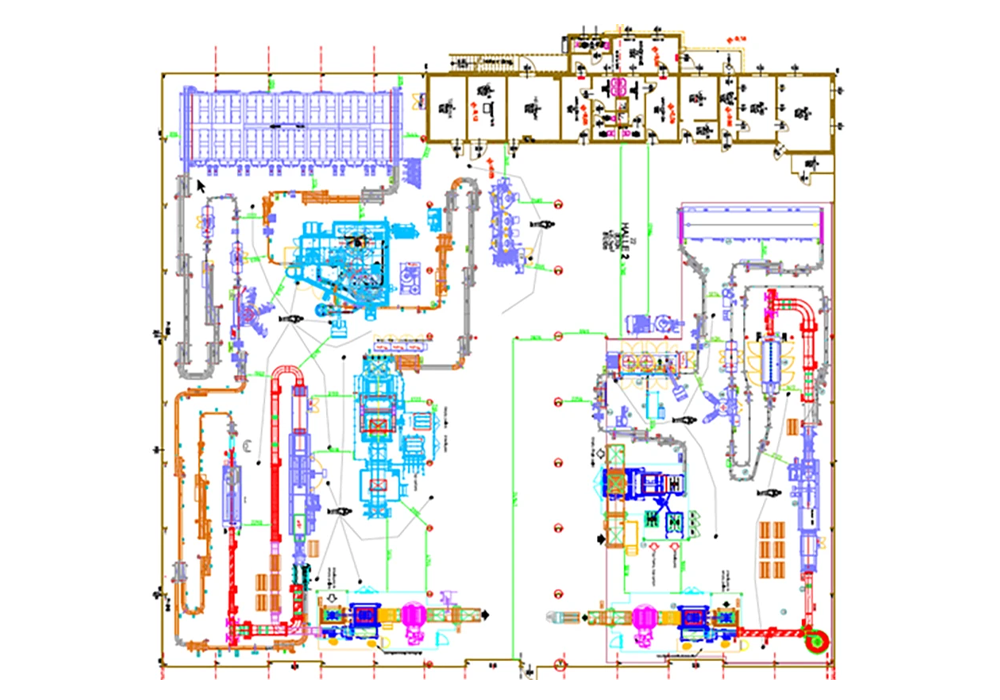
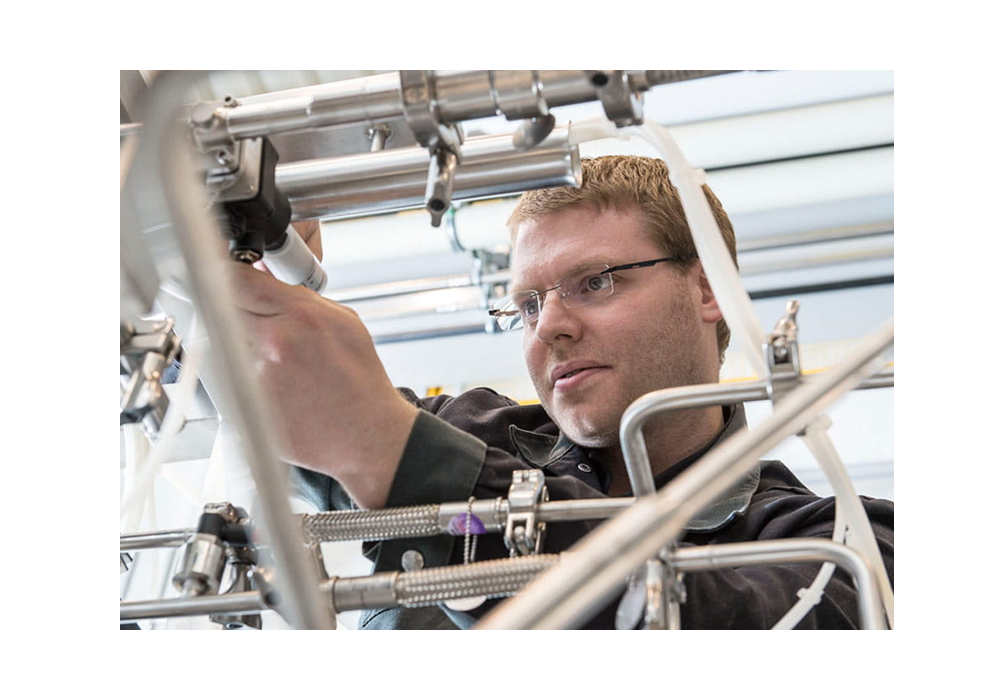
ALL-IN-ONE FILLING SOLUTIONS
The ALL-IN-ONE solutions are a user-friendly solution for filling beverages into cans, glass bottles and optionally PET.
Available in different sizes and configuration, the solutions are all purpose built for rinsing, filling, and closing with different closure types. We understand that no two customers will have the same needs or budgets, so we’ve developed systems that can be tailored to match just about every requirement. Customers can choose between several different filling systems, from a simple setup with exchangeable filling tubes, to a more sophisticated system that offers greater flexibility and faster change-over times.
It‘s an ideal solution for a wide range of products, including still and carbonated soft drinks, beer, still and sparkling wine, and other hot and cold beverages.
The flexible filling systems make it simple and fast to switch between bottle formats.
Built for optimum hygiene and operator safety, the ALL-IN-ONE can be washed using water or foam. For more sensitive products the filler can be built into clean execution, with advanced cleaning options and container and closure sterilization.
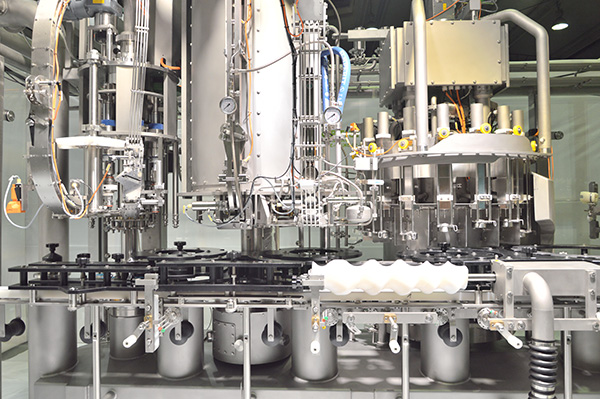
for cans, glass bottles and optionally PET
capacity range: 5.000 – 30.000 bph
16 - 110 filling valves
w/wo rinser
upgradeable with hot fill
(clean room execution and avinage function)
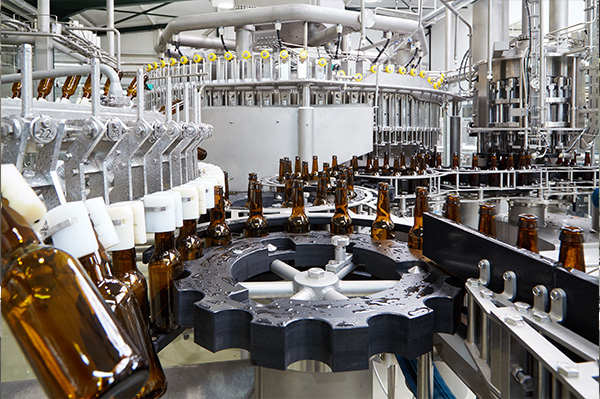
for glass bottles and optionally PET
Capacity range: 5.000 – 40.000 bph
16 - 120 filling valves
w/wo rinser
upgradeable with hot fill
(clean room execution and avinage function)
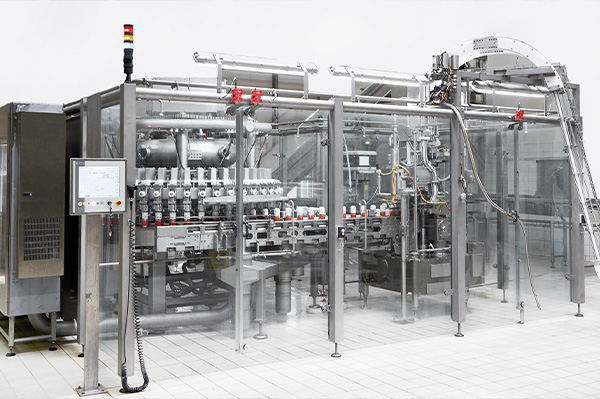
for cans
Capacity range: 5.000 – 50.000 cph
16 - 100 filling valves
w/wo rotary or gravity rinser
upgradeable with hot fill
(ultra-clean execution and avinage function)
SMALL-IN-ONE FILLING SOLUTIONS
Based on the proven ALL-IN-ONE platform but smaller in footprint, the SMALL-IN-ONE is an affordable and cost-effective solution but fully featured option for rinsing, filling and closing for smaller production and filling runs, or of where the space is limited. It offers largely standardized configurations in 3 different sizes (16, 24 or 32 filling valves), which makes it fast to install (2 weeks to first saleable product) with simple operation. Although standardized, it is also customizable and upgradable.
Built to match the highest requirements for hygiene, the SMALL-IN-ONE is highly versatile. So, whether your products are beer, still or sparkling wine, water, ready to-drink products or juices (even hot fill), the unit and filling valves can easily be set up.
The SMALL-IN-ONE uses reliable mechanical drives (instead of servo drives) that is an economical solution and independent of difficult supply conditions. Therefore, the solution can be delivered in under 6 months of order.
The solution has also been designed to reduce the environmental impact. It is equipped with a water recirculation system that uses the same water in 3 different operations, an optimized use of CO2 while keeping market-standard O2 pick-up levels.
for cans, glass bottles and optionally PET
capacity range: 5.000 – 10.000 cph
16-32 filling valves
w/wo rinser
hot fill as an option
for glass bottles and optionally PET
capacity range: 5.000 – 10.000 bph
16-32 filling valves
w/wo rinser
hot fill as an option
for cans
capacity range: 5.000 – 15.000 cph
16-32 filling valves
w/wo (rotary) rinser
hot fill as an option
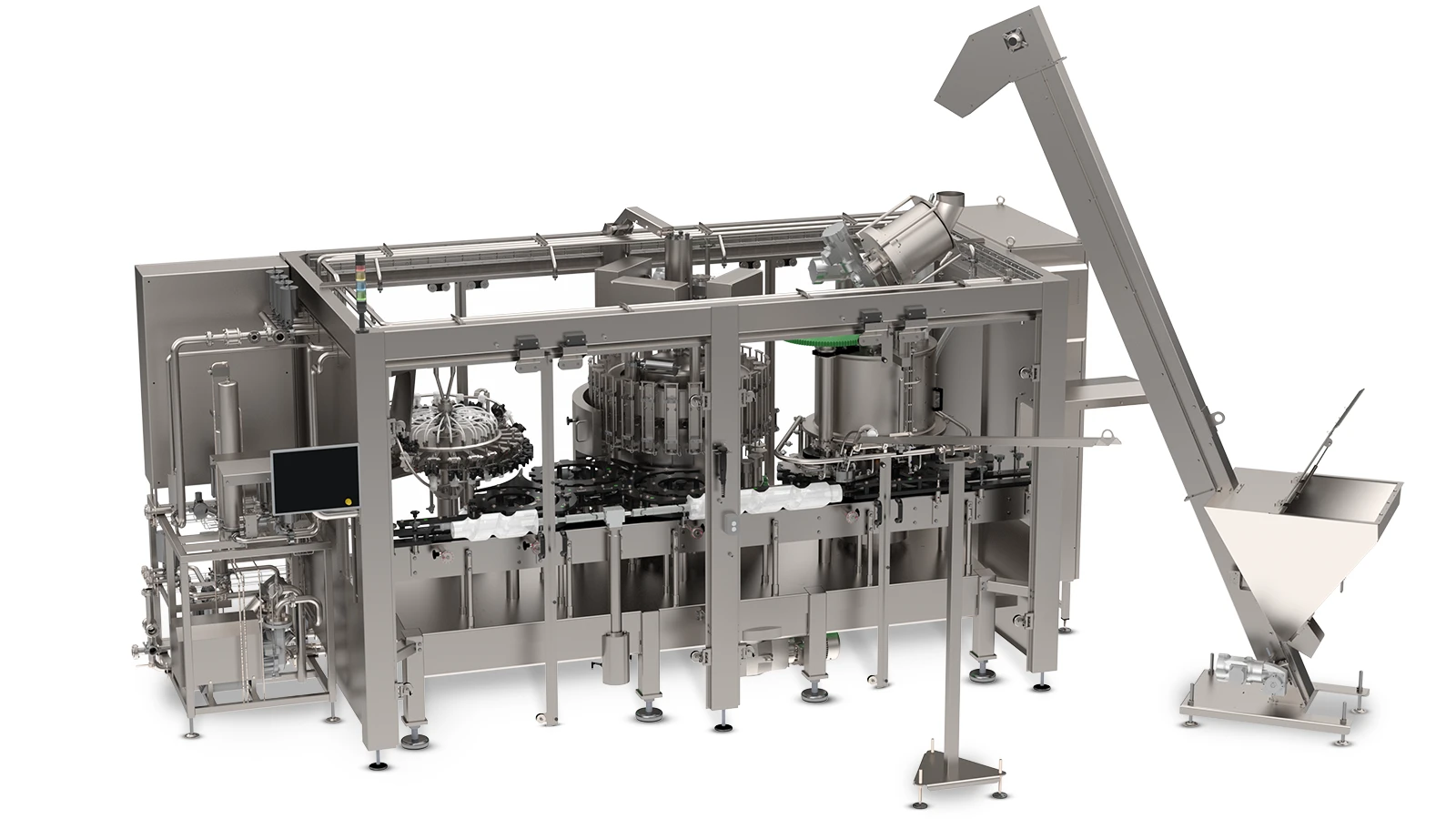
PROCESS EQUIPMENT
The product quality is the most important aspect for our customer. Therefore VIPOLL does not only offer flexible and reliable filling solutions, but process equipment for product preparation as well.
Our process solutions are individually engineered and tailored to customer-specific requirements and available spatial conditions.
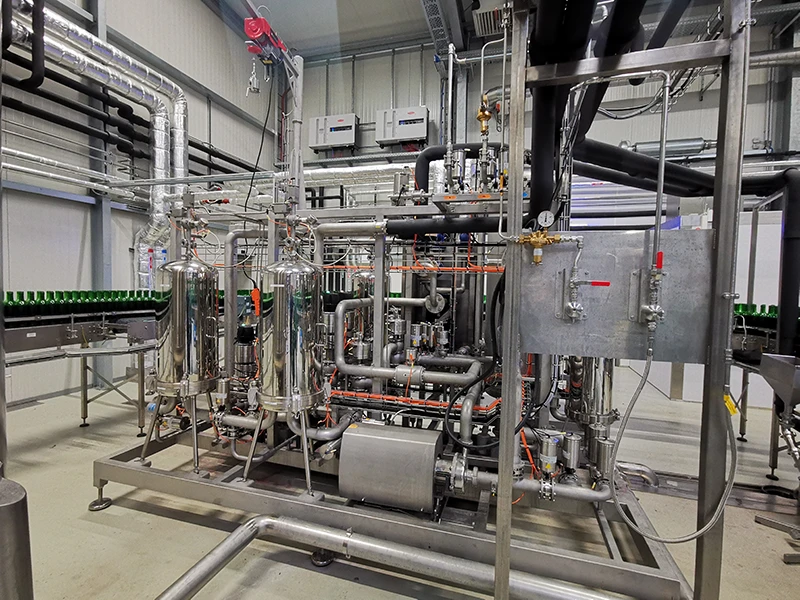
single line or multiline
sterile filtration
pre-filtration
option: Integrated stand-alone
CIP station for filtration
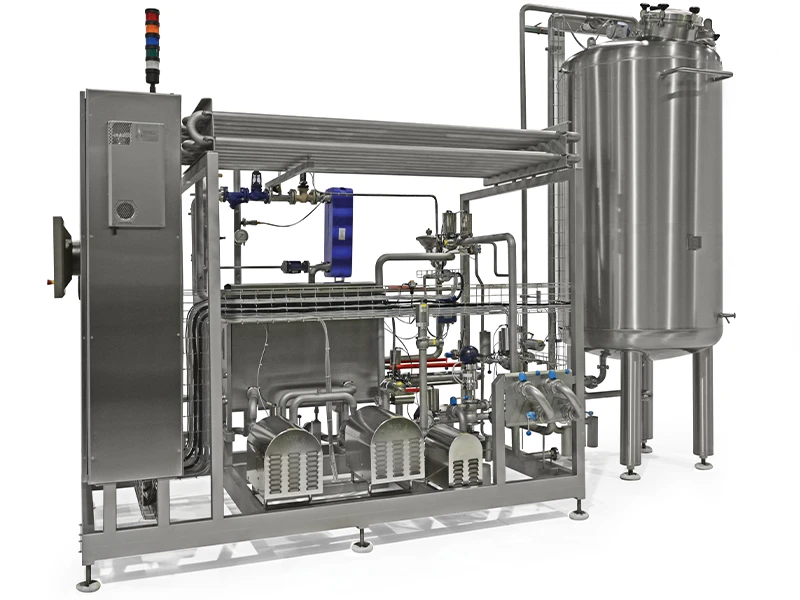
flexible solutions for beer, hot fill & cold fill soft drinks and UHT
accurate PE control
for different products, with different types of heat exchangers
w/wo (rotary) rinser
hot fill as an option
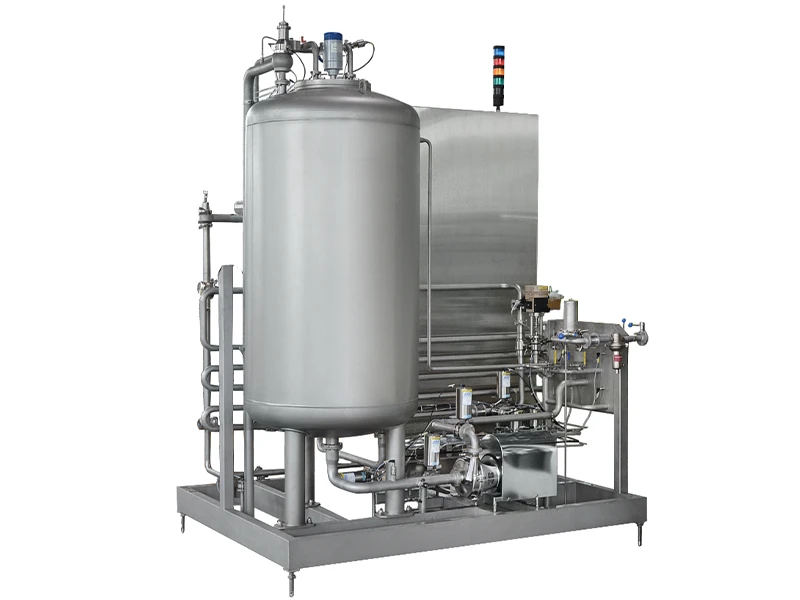
application for multiple beverages
CSD mixing and carbonation:
- high dosing accuracy for syrup and CO2
- real time dosing corrections for CO2 and Brix following sensor readouts
option: in-line water degassing system
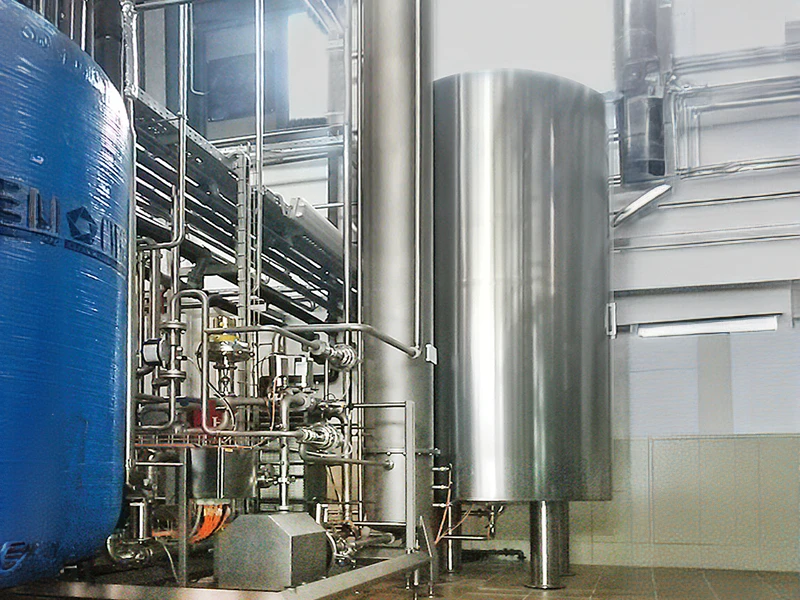
high flexibility adapted to requirements (process or product)
column degassing for high gravity brewing, residual oxygen <0.025 ppm
vacuum degassing for soft drink production for the finished product <1.0ppm
stripping gas either N2 or CO2
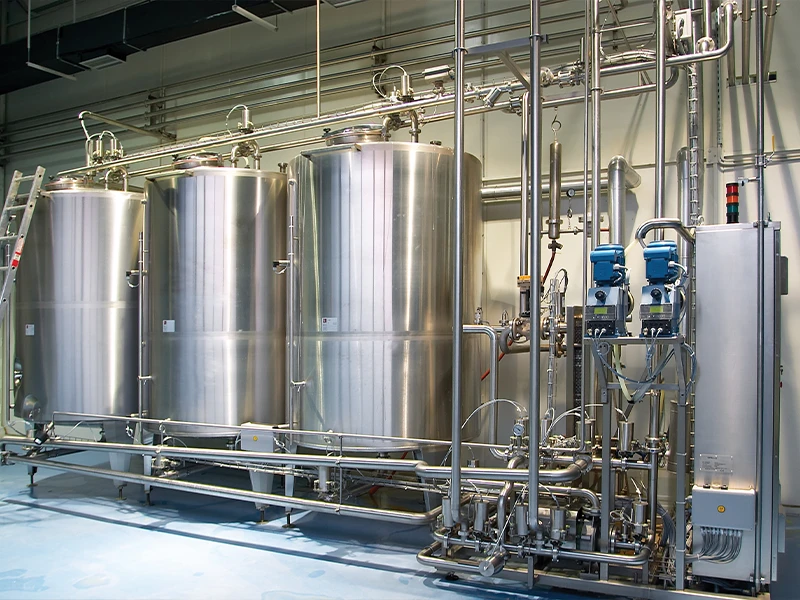
applications for multiple beverages
single or multiline stations
fitting number of CIP tanks
chemical + disinfection
automatic (CD, T*, flow, time) or manual execution
several independent CIP circuits (internal and external)
real time CIP-ing quality check-up
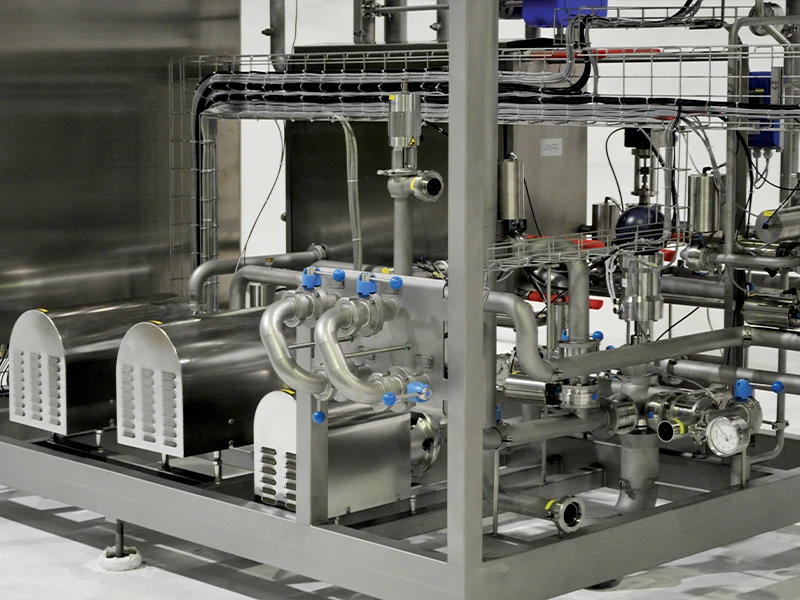
yeast dosing
color dosing
hot & cold product deaeration
changeable holding zone for different PUs
LINE INTEGRATION
VIPOLL doesn‘t just supply stand-alone equipment and automation. We really understand the industry and our customer‘s processes, products and challenges. We offer line engineering expertise for your whole process, upstream and downstream of our products. Our experts can work with you to design and configure the process and filling and packaging line. We‘ll offer our own equipment along with equipment of our trusted suppliers.
We‘ll adapt to Customer needs to make the journey less complex and give confidence in the quality and ultimately productivity of the plant.
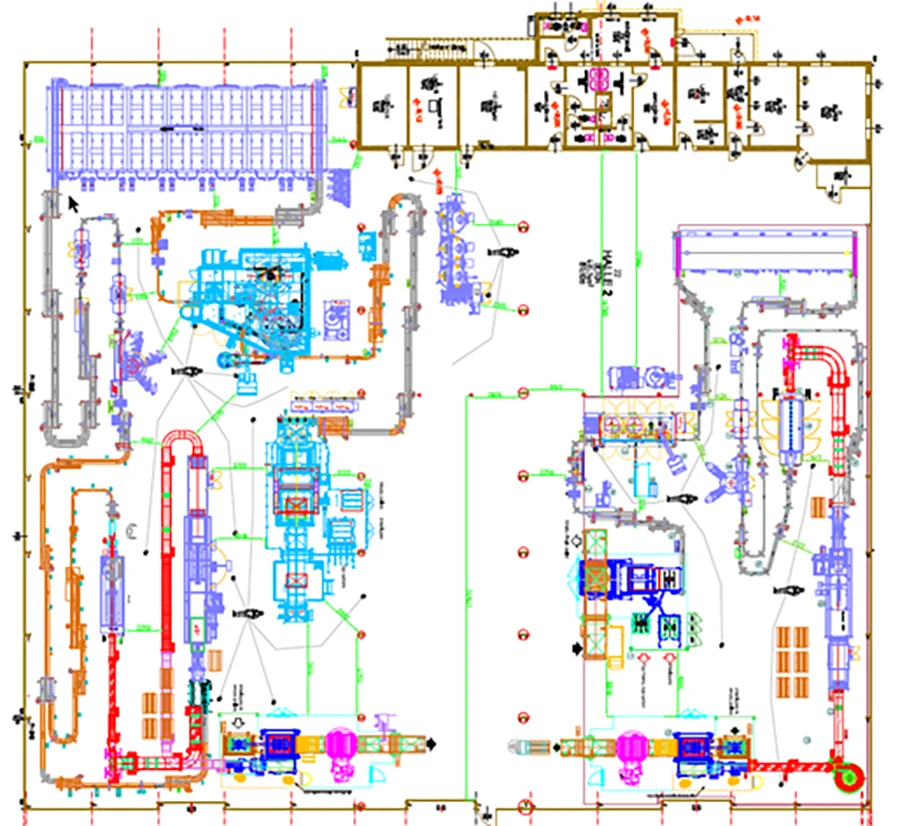
SERVICE & MAITENANCE
VIPOLL doesn’t stop at commissioning your new equipment. We offer personalized aftercare and service packages for the complete lifecycle of VIPOLL machines.
Our services and maintenance packages will take into account your products, processes and production hours, so we can help our customer to keep the plant running at peak performance.